زمینه های کاربردی تکنولوژی بریکت سازی
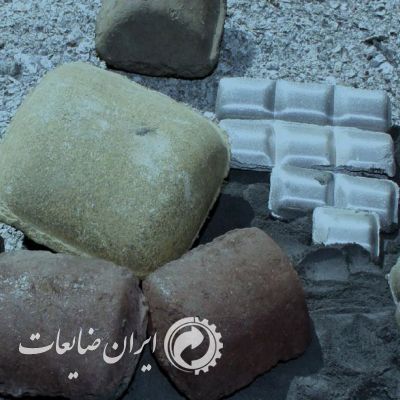
زمینه های کاربردی تکنولوژی بریکت سازی
تکنولوژی بریکت سازی از قدمتی حدود 200 ساله برخوردار بوده به طوری که صنایع مختلفی از آن ، جهت بهبود عملکرد فرآیند های خود استفاده می کنند فلسفه وجودی صنعت بریکت سازی را می توان استفاده بهینه از مواد جانبی و کم بازده تولید شده در صنایع مختلف عنوان نمود. اما در دهه اخیر کاربرد های جدیدی از صنعت بریکت سازی معرفی شده که اهمیت این صنعت را بیش از پیش نمایان کرده است.
در اکثر صنایع ، در حین فرآیند تولید همواره مقادیری مواد جانبی ایجاد می گردد که عمدتاً به واسطه دانه بندی ریز، امکان استفاده موثر از آنها وجود ندارد . لذا این مواد که گاهاً ارزش اقتصادی بالایی نیز دارند تنها به واسطه محدودیت های ابعادی ، نمی توانند مانند مواد دانه درشت تر مورد استفاده قرار گیرند. این موضوع می تواند اثرات منفی قابل توجهی بر راندمان تولید و همچنین توجیه پذیری اقتصادی فعالیت صنایع داشته باشد. در اینجاست که نقش تکنولوژی بریکت سازی نمایان شده به طوری که با کمک آن می توان استفاده موثر از مواد جانبی را میسر نمود. از جمله صنایعی که به طور گسترده از این تکنولوژی جهت بهبود عملکرد و افزایش راندمان تولید فرایندهای خود استفاده می کنند می توان به موارد زیر اشاره نمود :
- آهن و فولاد (آهن اسفنجی ، غبار واحد های احیای مستقیم و فولاد سازی ، پوسته های اکسیدی )
- مواد معدنی (زغال سنگ ، نمک ، دولومیت ، منگنز، فرو آلیاژ ها ، آلومینا ، آهک و...)
- مواد شیمیایی ( سولفات ها ، کربنات ها ، کلرید ها ، سیانید ها ، برومید ها و...)
- کود های شیمیایی کشاورزی
- مواد شوینده و بهداشتی
در ادامه به بررسی تعدادی از این صنایع خواهیم پرداخت.
همواره مقادیر قابل توجهی نرمه زغال سنگ به دست می آید (5 تا 10 درصد ) که همان طور که پیش تر اشاره گردید ، به واسطه محدودیت های ابعادی ، جهت استفاده موثر از آن ، از تکنولوژی بریکت سازی استفاده می شود. به طور کلی بریکت سازی زغال سنگ به واسطه اندازه ، شکل ظاهری و خواص فیزیکی _شیمیایی کاملاً یکنواخت ، رفتاری کاملا همگن در کاربرد مورد نظر داشته که تاثیر قابل توجهی بر افزایش راندمان مصرف انرژی و همچنین تسهیل در کنترل فرآیند و بهبود پایداری سیستم خواهد گذشت.
بریکت تراشه های فلزی
در حال حاضر بیشتر کارخانه های فرآوری فلزات و کارخانه های ریخته گری فولاد توجه کافی به تصفیه ضایعات و تراشه های فلزی ندارند. بیشتر ضایعات فلزی بصورت تصادفی روی هم چیده می شوند که این امر علاوه بر اتلاف منابع باعث آلودگی جدی محیط زیست نیز می شود به خصوص در بعضی از پشته های تراشه فلزی در فضای باز ، بیشتر تراشه های فلزی در کیسه ها یا جعبه های آهنی حمل می شوند و سپس توسط واگن برقی که تراشه های فلزی را حمل می کند ، به مکان های دیگر ارسال می شوند. در طول کل فرآیند ، تراشه های فلزی در مکان های مختلف سقوط می کنند و باعث آلودگی زمین و اتلاف منابع می شوند
دستگاه بریکت قراضه به طور گسترده ای در کارخانه های پروفیل آلیاژ آلومینیوم ، کارخانه های ریخته گری فولاد ، کارخانه های ریخته گری آلومینیوم ، کارخانه های ریخته گری مس و بیشتر ایستگاه های بازیافت منابع فلزات زباله استفاده می شود. این می تواند تراشه های آلومینیوم ، سوفاله فولادی ، پودر آهن ، تراشه های مس و سایر بریکت ها را به کوره بازگرداند.
صنعت احیای مستقیم
از دیگر زمینه های کاربردی صنعت بریکت سازی می توان به صنعت احیای مستقیم اشاره نمود.محصول خارج شده از کوره ی احیای مستقیم اشاره نمود.محصول خارج شده از کوره احیای مستقیم معمولا دارای 5 تا 5 1 درصد وزنی نرمه آهن اسفنجی ( با دانه بندی کمتر از 6 میلی متر ) بوده که به واسطه اندازه ریز آن ، استفاده مستقیم از این ماده در کوره فولاد سازی توجیه فنی و اقتصادی ندارد. در حدود نیم قرن است که از تکنولوژی بریکت سازی به عنوان راه حل این مشکل استفاده می شود. بدین صورت که محصول خروجی از کوره احیای مستقیم باعبور از سیستم اسکرین ، غربال شده و نرمه ریز دانه از محصول اصلی جدا می گردد. حال نرمه آهن اسفنجی توسط سیستم بریکت سازی به بریکت نرمه آهن اسفنجی تبدیل شده و قابلیت شارژ به کوره فولاد سازی را پیدا می کند.بدین ترتیب با بهره گیری از تکنولوژی بریکت سازی راندمان مصرف آهن اسفنجی به طور قابل توجهی بهبود پیدا خواهد نمود.
از طرف دیگر ، از دهه 80 میلادی انقلابی در صنعت آهن و فولاد رخ داد به طوری که با بهره گیری از تکنولوژی بریکت سازی دما بالا در واحد های واحد مستقیم ، محصولی با نام بریکت داغ آهن اسفنجی (HBI) پدید آمد که بسیاری از مشکلات پیرامون ذخیره سازی و حمل و نقل آهن اسفنجی و همچنین شارژ این محصول به کوره های فولاد سازی را مرتفع نموده است.
در طی چند سال اخیر نیز زمینه جدیدی در حوزه کاربرد تکنولوژی بریکت سازی در صنعت احیای مستقیم ایجاد شده که هدف از آفرینش آن تولید محصولی با کیفیت و در عین حال ، دارای خواص مورد نیاز واحد های فولاد سازی بوده است. این محصول که با نام بریکت سرد آهن و کربن (CBIC) شناخته می شود، در طی فرآیند بریکت سازی آهن اسفنجی در دماهای پایین تولید می گردد. از مزایای این محصول نسبت به آهن اسفجی ،می توان به استحکام خردایش و مقاومت به سایش بیشتر ، مقاومت به افت درجه فلزی بیشترو همچنین ریسک بسیار کمتر در حین ذخیره سازی و حمل ونقل اشاره نمود. از طرف دیگر ، در فرایند تولید این محصول، امکان افزودن افزودنی های مورد نیاز واحد فولاد سازی مثل کربن ،آهک و فرو آلیاژ ها و در نتیجه ، تنظیم ترکیب شیمیایی شارژ ورودی به کوره فولاد سازی نیز وجود دارد. تمام این مزایا موجب خلق ارزش افزوده قابل توجه نسبت به آهن اسفنجی می شود که صنعت احیای مستقیم را همیشه مدیون تکنولوژی بریکت سازی کرده است.
صنعت تولید منیزیم
یکی از روش های اصلی تولید شمش منیزیم فرآیند پیجن (PIDGEON) بوده که اساس آن ، احیای سنگ منیزیم با استفاده از سیلیکون (سیلیکوترمی) می باشد. در این فرایند ابتدا سنگ دولومیت با دانه بندی مناسب به کوره های دوار شارژ شده و در دماهای بالا کلسینه می شود. سپس در دولومیت کلسینه شده به همراه فروسیلیس (عمل احیائی ) و فلورین (به عنوان کاتالیزور واکنش احیاء ) توسط بال میل به شکل پودر در می آیند. حال جهت ایجاد سطح تماس بهینه بین دولومیت ، فروسیلیس و فلورین ، و همچنین جهت تسهیل در انجام مراحل پایانی فرآیند ، مواد مذکور به ماشین بریکت سازی وارد شده و به بریکت تبدیل می شوند . سپس بریکت ها به محفظه احیاء (Retort ) شارژ شده و پس از اعمال خلاء ، برای مدت حدود 12 ساعت در دمای 1200 درجه سانتی گراد نگهداری می شوند.
پس از این مرحله ، تاج های منیزیمی تولید شده در ریتورت ها خارج شده و در کوره های ذوب ، به شمش منیزیم تبدیل می گردند. همان طور که اشاره گردید، عملیات بریکت سازی در این فرآیند موجب بهبود پایداری سیستم ، بهبود سنتیک انجام واکنش های احیاء و تسهیل در عملیات شارژ و تخلیه مواد خواهد شد.
فرآوری سنگ منگنز
سنگ منگنز استخراج شده از معادن منگنز معمولاً دارای عیار پایینی بوده که جهت پرعیار سازی آن از روش هایی مانند جدایش ثقلی و جدایش مغناطیسی استفاده گردد. در پایان فرآیند فرآوری سنگ منگنز، محصول به دست آمده معمولاً حاوی مقادیر قابل توجهی مواد ریز دانه ( با دانه بندی 100 تا 500 میکرون ) می باشد که استفاده مستقیم آن در کوره فولاد سازی توجیه فنی و اقتصادی ندارد.لذا با استفاده از تکنولوژی بریکت سازی یا فشرده سازی (Compaction_Granulation) می توان ابعاد نرمه های مذکور را به گونه ای تنظیم نمود که قابلیت استفاده موثر از آنها ایجاد شود. بدین ترتیب هم راندمان واحد فرآوری سنگ منگنز به طور چشمگیری افزایش می یابد و هم از ورود مقادیر زیادی نرمه و غبار به محیط زیست جلوگیری خواهد شد.
صنعت آهک سازی
آهک (CAO) از جمله مواد پرکاربردی ای است که در اغلب صنایع از جمله صنایع تولید فلزات ، صنایع تصفیه آب و فاضلاب و صنایع راه و ساختمان مورد استفاده قرار می گیرد. آهک از فرآیند تکلیس (Calcination) سنگ آهک (CaCO3) در کوره های دوار به دست می آید.همواره در فرآیند تولید و جابجایی آهک حدود 10 تا 20 درصد نرمه آهک ( با دانه بندی کمتر از 6 میلیمیتر) ایجاد می گردد. یا اینکه نرمه آهک قابلیت استفاده در برخی از صنایع مثل تصفیه آب و فاضلاب را دارد، اما معمولاً حجم نرمه تولید شده بیش از نیاز صنایع مورد نظر بوده و همواره مازاد نرمه در واحد های تولید آهک وجود دارد. بدین ترتیب با استفاده از تکنولوژی بریکت سازی می توان دانه بندی نرمه آهک را به گونه ای تنظیم نمود که قابلیت استفاده در صنایع پایین دست را داشته باشد. بدین ترتیب با استفاده از تکنولوژی بریکت سازی ، حجم قابل توجهی از مواد جانبی موجود در واحد های تولید آهک ، به محصولی با ارزش افزوده بالا و خواص مطلوب تبدیل خواهند شد.
صنعت تولید سولفید سدیم
سولفید سدیم (Na2s) از جمله مواد پرکاربردی است که در صنایع شیمیایی ، کاغذ سازی و چرم سازی مورد استفاده قرار می گیرد . فرایند تولید سولفید سدیم، احیای کربوترمی سولفات سدیم (Na2So4 ) است ، بدین صورت که سولفات سدیم و زغال سنگ در کوره زمینی شارژ شده و در اثر انجام واکنش احیاء ، محصول سولفیدی به دست می آید. اما در طی فرآیند استخراج سولفات سدیم از معادن ، معمولا مقادیر قابل توجهی مواد ریز دانه سولفات تولید می گردد. شارژ مستقیم این مواد ریزدانه به کوره زمینی موجب خروج مقادیر قابل توجهی از انها از طریق گاز خروجی کوره خواهد شد که کاهش راندمان فرآیند و افزایش میزان تولید آلاینده های محیط زیستی را در پی خواهد داشت.
در حال بهره گیری از تکنولوژی بریکت سازی یا فشرده سازی در واحد های استخراج سولفات سدیم و افزایش دانه بندی مواد ریز دانه تولید شده در آنها موجب بهبود عملکرد کوره احیاء و افزایش راندمان مصرف اولیه می گردد.
نظرات کاربران :