برخی مشکلات رایج در فرآیند تزریق پلاستیک
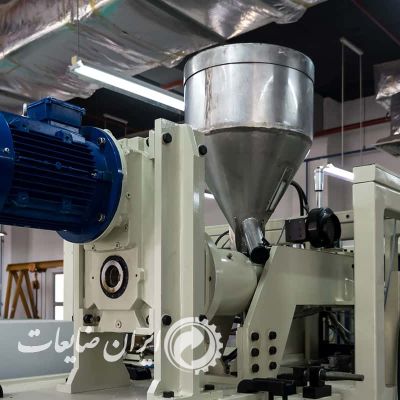
مقدمه
یکی از روش های مهم و اصلی در تولید انواع محصولات پلاستیکی، روش تزریقی است. برای این منظور از دستگاه تزریق پلاستیک استفاده می شود. این دستگاه کمک شایانی به صنعت پلاستیک کرده اما با این حال مشکلات مختلفی در فرآیند تولید وجود دارد که می تواند کیفیت محصول نهایی را تحت تاثیر قرار دهد. در این مطلب به بررسی برخی از این مشکلات خواهیم پرداخت.
ایجاد خطوط جریان روی پلاستیک
یکی از رایج ترین مشکلات دستگاه تزریق پلاستیک ایجاد خطوط جریان روی محصول پلاستیکی است. به این صورت که خطوطی موج دار روی پلاستیک تشکیل می شوند.
علت ایجاد خطوط جریان روی پلاستیک
دلایل مختلفی برای تشکیل خطوط جریان روی پلاستیک وجود دارد. شتاب بالای پر شدن قالب به خاطر شکل خاص محصول از جمله این دلایل می باشد. در صورتی که دمای مواد پلاستیکی و قالب بیش از حد پایین باشد هم این مشکل پیش می آید. سرعت و فشار تزریق پایین نیز از دیگر علل ایجاد این مشکل است.
راهکارهایی برای جلوگیری از ایجاد خطوط جریان
به منظور جلوگیری از ایجاد خطوط جریان روی محصولات و قطعات پلاستیکی در فرآیند تزریق پلاستیک می توان اندازهی چاه های خنککننده در کانال عبور مواد مذاب را افزایش داد. علاوه بر این می توان اندازهی معبرها و دریچهها را هم افزایش داد.
اگر کانال اصلی کوتاه تر شود نیز این مشکل ایجاد نمی شود. راهکار هایی همچون بالا بردن سرعت تزریق هم موثر می باشد. بیشتر نمودن دمای قالب و مواد تزریق، افزایش فشار و زمان نگهداری فشار از دیگر راهکار های پیشنهادی هستند.
ایجاد فرو رفتگی در محصول و علت آن
مشکل دیگری که در فرآیند تزریق ممکن است به وجود آید، ایجاد فرو رفتگی در قطعه می باشد. عواملی همچون پایین بودن بیش از حد فشار تزریق، بالا بودن بیش از حد دمای ذوب و دمای قالب نقش مهمی در ایجاد آن دارند. اگر ساختار قطعات، طراحی مناسبی نداشته باشد و یا در صورتی که زمان خنک شدن قطعه خیلی کوتاه باشد هم ممکن است فرورفتگی ایجاد گردد.
رفع مشکل فرو رفتگی
برای اینکه قطعات پلاستیکی تولید شده دچار فرورفتگی نشوند می توان در قسمت هایی که احتمال ایجاد این مشکل وجود دارد، صفحات شیار دار استفاده کرد. کاهش نسبت ابعاد کار و اندازه دیواره ضخیم، افزایش فشار تزریق و دستگاه هم پیشنهاد می شود.
تغییر موقعیت دریچه ها و افزایش دادن اندازه آنها راهکار های مناسبی هستند.
ایجاد حباب، علت و راهکار
به دام افتادن مولکول های هوا در حفره تزریق باعث ایجاد حباب در محصولات پلاستیکی تولید شده به روش تزریقی می گردد. برای جلوگیری از تشکیل حباب می بایست تا حد امکان ناهمواری هایی که در قطر دیواره ها وجود دارد از بین بروند و دیواره ها، ضخامت یکدستی داشته باشند.
آخرین قطعهای که با مواد تزریقی پر میشود، به منافذ تهویه مجهز گردد.
در آخرین مرحله، سرعت تزریق ، کاهش یابد. کاهش دمای قالب هم در رفع این مشکل کمک خواهد کرد.
خط جوش، علت و راهکار
پیدا شدن خطوط جوش روی محصولات پلاستیکی هنگام جوش خوردن دو قطعه نیز از مشکلات رایج می باشد که در اثر وجود منافذ و فضاهای خالی، ناهمواری ضخامت دیوارهها و استفاده از روش چند دریچهای تزریق ایجاد می شود.
به منظور جلوگیری از چنین مشکلی باید موقعیت دریچه ها تغییر نمایند. میزان فاکتور های آزاد، کم تر شود. غلظت مواد مذاب کاهش یابد و قالب دارای منافذ تخلیه باشد.
ایجاد سوختگی در قطعات پلاستیکی
وقتی دمای ذوب، خیلی بالا باشد سبب تخریب مواد شده و ردی از سوختگی روی قطعه پلاستیکی ایجاد می شود. همچنین در صورت عدم خروج به موقع گازهای موجود در حفرههای تزریق هم این مشکل رخ می دهد. اگر سیستم رانر به درستی طراحی نشود و همین طور بالا بودن سرعت پیچ های ریخته گری، مشکل سوختگی، بسیار محتمل است.
برای جلوگیری از ایجاد سوختگی در محصولات پلاستیکی باید اندازه معابر را افزایش و سرعت و فشار تزریق را کاهش داد. در قسمت های که میزان تولید گاز بیشتر است، خروجی در نظر گرفته شود. هیتر و ترموکوپل ها از نظر سالم بودن بررسی شوند. دمای بشکه نیز باید پایین باشد.
ناقص بودن قطعه پلاستیکی
در برخی مواقع، قطعه پلاستیکی تولید شده ناقص است که می تواند به دمای بسیار پایین مواد مذاب و یا فشار و سرعت کم تزریق مربوط باشد. اگر حفره به صورت ضعیف تخلیه گردد و یا پلیمر قبل از موعد ذوب شود، قطعه تولید شده ناقص خواهد بود. اگر مواد خام رقت کافی نداشته باشند هم ممکن است قطعه ناقص تولید شود.
در صورتی که قطعه، خیلی باریک و دریچه ها خیلی کوچک باشند امکان ناقص بودن قطعه تولیدی بیشتر می شود.
راهکار هایی که برای مرتفع نمودن آن وجود دارد شامل موارد زیر است:
- پر کردن دیوار ه های ضخیم قبل از دیواره های نازک
- استفاده از مواد مایع بیشتر
- افزایش تعداد دریچه ها
- افزایش اندازه معابر
- افزایش حجم تزریق
- افزایش سرعت و فشار تزریق
- بالا بردن دمای سیلندر و قالب
- بررسی سوپاپ و دیوارههای داخلی سیلندر از نظر عدم فرسودگی
پلیسه شدن قطعات پلاستیکی
بیرون زدن پلاستیک اضافه از قالب سبب می شود تا یک بخش اضافه روی محصول ایجاد گردد که به آن پلیسه می گویند. این مشکل که بسیار رایج است در اثر فشار ناکافی برای بستن قالب، طراحی نامناسب سیستم تخلیه، قالب ریزی در شرایط نامناسب و وجود نقص در قالب به وجود می آید.
با استفاده از قالب هایی با طراحی استاندارد، تمیز نمودن سطح قالب، کم کردن دمای بشکه و نازل، کاهش فشار و سرعت تزریق و افزایش زمان تزریق می توان این مشکل را به حداقل رساند.
نظرات کاربران :